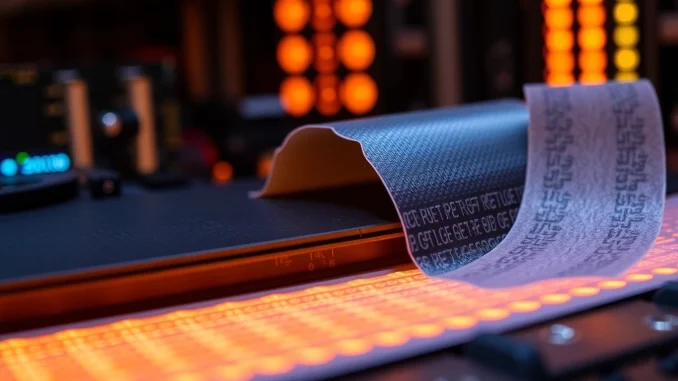
Understanding Thermal Management Materials
Definition and Importance of Thermal Management
Thermal management materials are essential components in the design and operation of electronic devices. They facilitate the effective dissipation and control of heat generated during electronic operations, which is crucial in maintaining optimal performance and ensuring the reliability of devices. When components generate excessive heat, it can lead to reduced efficiency, premature failure, or even catastrophic damage. Therefore, the strategic use of thermal management materials plays a pivotal role in the effective functioning of various applications, particularly in high-performance environments.
Types of Thermal Management Materials
Thermal management materials can generally be categorized into several distinct types based on their application and the method they utilize to manage heat. Key categories include:
- Thermal Interface Materials (TIM): These materials improve thermal contact between heat-generating components and heat sinks, enhancing heat transfer efficiency.
- Gap Fillers: Designed to fill spaces between components or their surfaces, gap fillers ensure that any air gaps that may impede heat transfer are eliminated.
- Phase Change Materials: These materials absorb and release heat as they change states, providing excellent temperature control across varying operational conditions.
Applications in Electronics
The applications of thermal management materials extend across different sectors within electronics. For instance, in consumer electronics such as smartphones and laptops, effective thermal management is crucial to maintain performance and extend device longevity. In automotive applications, these materials are vital in managing heat in electric vehicles and internal combustion engines, thus contributing to performance and safety. Furthermore, thermal management is significant in industrial equipment, telecommunications, and power electronics where thermal regulation directly impacts system reliability and operational efficiency.
Key Benefits of Using Thermal Management Materials
Enhanced Device Performance
The utilization of thermal management materials leads to enhanced device performance by facilitating optimal thermal conduction and dissipation. Devices such as GPUs and CPUs particularly benefit from these materials as they require sustained performance under high workloads. High-quality thermal interface materials help in maintaining lower temperatures, enabling peak performance and preventing thermal throttling, which can hinder operational capability.
Reduced Thermal Resistance
One of the prime advantages of thermal management materials is their ability to reduce thermal resistance. By improving heat transfer pathways within electronic assemblies, these materials help lower the temperature variations across components. This reduction in thermal resistance not only improves system efficiency but minimizes the overall energy consumption. Various types of TIM and gap fillers are specifically engineered to provide lower thermal resistance, thereby allowing devices to operate cooler and more efficiently.
Longevity of Electronic Components
Excessive heat can shorten the lifespan of electronic components, leading to increased maintenance costs and device failures. Thermal management materials enhance the longevity of devices by mitigating overheating risks. When employed effectively, these materials contribute to consistent operating temperatures, thereby preserving the integrity and functionality of critical components. This longevity is crucial in high-stakes environments like aerospace, where system failures can have severe consequences.
Common Types of Thermal Management Materials
Thermal Interface Materials (TIM)
Thermal interface materials serve as a conduit for heat transfer between heat-generating components and heat sinks. They fill microscopic air gaps between surfaces, facilitating a more efficient thermal pathway. Types of TIMs include thermal pastes, pads, and adhesives, each with specific thermal conductivity properties suited for various applications. Selecting the right TIM involves evaluating factors such as thermal conductivity, viscosity, and application method.
Gap Pads and Tapes
Gap pads are soft, compliant materials designed to fill gaps between components, ensuring maximum contact area and thermal transfer. They are available in various thicknesses and thermal conductivities, providing options for diverse assembly requirements. Thermal tapes, on the other hand, are adhesive films that bond components while providing adequate thermal dissipation. Both gap pads and thermal tapes are vital for applications where mechanical stress and vibration could otherwise compromise thermal pathways.
Phase Change Materials
Phase change materials (PCMs) are unique in their ability to absorb and release heat during their phase transition from solid to liquid and vice versa. They can maintain stable temperatures by storing excess heat and gradually releasing it when temperatures drop. This property makes PCMs ideal for applications requiring temperature regulation across varying conditions, such as thermal batteries and thermal management in electric vehicles.
Selecting the Right Thermal Management Material
Factors to Consider
When selecting thermal management materials, several factors must be considered, including:
- Thermal Conductivity: This indicator determines the efficiency of heat transfer; materials with higher conductivity provide better performance.
- Mechanical Properties: Factors such as stiffness and compliance affect how well the material can interface with various components.
- Temperature Range: Ensure the material can operate effectively within the required temperature limits of the application.
Performance Metrics
Performance testing of thermal management materials is crucial for ensuring they meet application requirements. Common evaluation metrics include:
- Thermal Resistance: measured in degrees Celsius per Watt (°C/W), indicates how effectively the material conducts heat.
- Thermal Conductivity: quantified in Watts per meter Kelvin (W/mK), provides a measure of a material’s ability to conduct heat.
- Dielectric Strength: important for electrically insulating materials, ensuring safety and preventing electrical failures.
Compatibility and Application Requirements
It is also essential to assess the compatibility of the thermal management material with the surrounding environment. Considerations include chemical resistance, moisture absorption, and expansion coefficients. Additionally, materials must be chosen based on the specific application requirements—whether they facilitate easy installation, withstand extreme conditions, or accommodate specific mechanical loads.
Future Trends in Thermal Management Materials
Innovations in Material Science
The field of thermal management materials is ever-evolving, with continuous innovations paving the way for enhanced performance. Advancements in nanotechnology and composite materials are leading to the development of lighter, more effective solutions. Research is ongoing into materials that combine thermal management with other functionalities, such as electrical conductivity and structural integrity, which could improve overall system performance.
Sustainable Thermal Solutions
As industries move towards more sustainable practices, the demand for eco-friendly thermal management materials is rising. Solutions that reduce reliance on toxic substances while maintaining efficacy are under investigation. This includes the development of bio-based thermal materials and the recycling of existing materials, contributing to a circular economy in manufacturing.
Impact of Technology Advancements
Technology advancements, particularly in electronics, are driving the need for more efficient thermal management solutions. As devices become faster, smaller, and more powerful, the requirements for thermal regulation will continue to evolve. Innovations such as advanced thermal simulation tools and AI-driven design processes enable more precise material selection, ensuring that thermal performance aligns with design benchmarks.
Leave a Reply