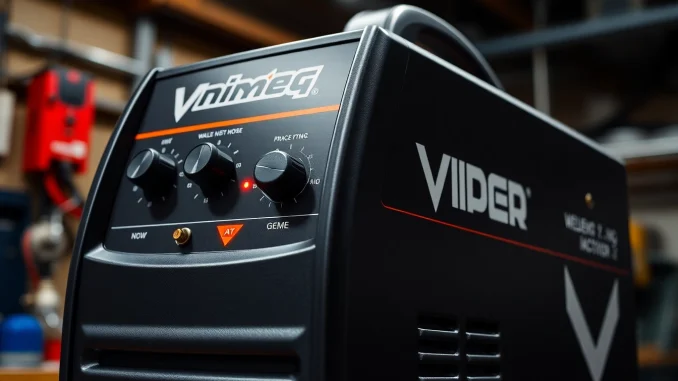
Introduction to the Unimig Viper Series
In the world of welding, versatility and reliability are paramount. One brand that has consistently delivered on these demands is Unimig, particularly with its unimig viper series. Designed for both enthusiasts and professionals, the Unimig Viper series offers a range of multi-process welders that cater to different welding applications while maintaining ease of use and portability. This comprehensive guide will delve into the features, advantages, and comparisons of the Unimig Viper series, particularly focusing on the Viper 185 model, ensuring you have all the knowledge required to make informed decisions regarding your welding needs.
What is the Unimig Viper?
The Unimig Viper series represents a line of advanced welding machines that provide MIG, TIG, and Stick capabilities in a single package. These welders are designed with inverter technology, enabling them to be lightweight, efficient, and easy to transport. The Viper series is particularly revered for its user-friendly interface, which is ideal for both beginners and experienced welders. The series supports a variety of materials, making it a versatile addition to any workshop or job site.
Key Features of the Unimig Viper
When exploring the Unimig Viper series, several key features stand out:
- Multi-Process Capabilities: Each Viper machine can perform MIG, TIG, and Stick welding, allowing users to tackle diverse projects without switching machines.
- Error-Free Synergic Setting: The machines are equipped with synergy settings that automatically adjust parameters for optimal performance based on the material type and thickness.
- Portability: The compact and lightweight design makes it easy to transport the Viper machines to various job sites, enhancing their practical application.
- User-Friendly Interface: The intuitive controls and displays simplify operation, making it accessible for novice welders while still offering advanced features for professionals.
- Durability: Built with high-quality materials and innovative designs, Viper machines are constructed to withstand rigorous use.
Who Should Use the Unimig Viper?
The Unimig Viper series is tailored for a wide audience:
- DIY Enthusiasts: Hobbyists looking to tackle home projects will find the Viper series user-friendly and effective for various applications.
- Small Business Owners: For welders running small fabrication jobs or repair services, the multi-process capabilities allow for flexibility without the need for multiple machines.
- Industrial Applications: Professionals in need of dependable and portable welding solutions for on-site work will benefit from the Viper’s mobility and performance.
Understanding the Welding Processes
To fully grasp the capabilities of the Unimig Viper series, it’s crucial to understand the three primary welding processes it supports: MIG, TIG, and Stick welding.
MIG Welding: A Beginner’s Overview
MIG welding, or Metal Inert Gas welding, is a process that uses a continuous wire feed to create a weld. The wire acts as both the electrode and the filler material, which simplifies the welding process. This technique is favored for its speed and ease of use, making it an excellent choice for beginners. The Unimig Viper series supports both gas shielded and gasless MIG welding, allowing users to operate in various environments.
TIG Welding: Precision and Control
TIG welding, or Tungsten Inert Gas welding, is known for its precision and ability to produce high-quality welds. It involves a non-consumable tungsten electrode, and the welder must manually add filler material. This process is ideal for thin materials and for applications requiring a strong aesthetic finish. The Viper series is capable of performing TIG welding, making it suitable for delicate projects or materials like aluminum.
Stick Welding: Strength and Versatility
Stick welding, or Shielded Metal Arc Welding (SMAW), uses a coated electrode to produce the weld. This method is robust and versatile, making it ideal for outdoor work and in situations where wind may affect other welding types. The Unimig Viper can also function effectively in Stick welding mode, giving users the ability to work in various conditions.
Comparing Unimig Viper Models
In the Unimig Viper series, each model may offer varying features suited to different user needs. Understanding the distinctions can help you find the right machine for your projects.
Unimig Viper 185: Performance Insights
The Unimig Viper 185 is a standout model within the series. It offers seamless multi-process functionality and delivers up to 185 amps of welding power, making it suitable for a wide range of materials, including mild steel, stainless steel, and aluminum. The machine’s synergic control means that it can automatically adjust settings based on the selected wire size and material thickness, simplifying the user experience significantly. The Viper 185 is compact yet powerful, perfect for mobile professionals and home workshops alike.
Unimig Viper 165 vs. 185 Analysis
When comparing the Viper 165 and Viper 185 models, the most notable differences lie in power output and weight:
- Power Output: The Viper 185 provides a higher amp output than the 165, allowing for more versatility in thicker materials.
- Portability: The 165 model is slightly more lightweight, making it easier to transport for quick jobs.
- Price Point: The Viper 165 generally comes at a lower price point, making it an excellent choice for budget-conscious users who may not require the additional power of the 185.
Choosing the Right Viper for Your Needs
When selecting between various models in the Unimig Viper series, consider the following factors:
- Project Requirements: Assess the materials and thicknesses you plan to work with. If you require a higher output for thicker materials, the Viper 185 may be more appropriate.
- Portability: If you frequently move your equipment, weigh the model’s weight and compactness.
- Experience Level: Beginners may benefit from the Viper 165 for its simplicity, while more experienced welders may appreciate the performance capabilities of the Viper 185.
Best Practices for Using the Unimig Viper
To maximize the performance and lifespan of your Unimig Viper welder, adhering to best practices during setup, operation, and maintenance is essential.
Setting Up Your Welder
Proper setup of your Viper welder is crucial for achieving optimal performance. Here are important steps to follow:
- Read the Manual: Every Viper welding machine comes with a detailed manual. Understanding the specifications and recommended settings will ensure safer and effective welding.
- Check Connections: Inspect all connections and ensure that your power source meets the welder’s requirements. Proper grounding is crucial for safety and performance.
- Correct Wire Choice: Depending on the welding mode, select the appropriate wire for your project. Ensure compatibility with the material being welded.
Safety Tips while Welding
Welding presents various hazards, making safety a priority. Here are key safety tips:
- Protective Gear: Always wear the appropriate protective gear, including welding helmets, gloves, and fire-resistant clothing.
- Ventilation: Ensure proper ventilation while welding, especially when using gas. Fumes can be hazardous to health.
- Fire Safety: Keep flammable materials away from your workspace, and have fire extinguishing equipment readily available.
Maintenance to Extend Lifespan
Regular maintenance can prolong the life of your Unimig Viper welder:
- Clean the Machine: After each use, clean any weld spatter and debris from the machine to prevent damage.
- Inspect Cables: Regularly check cables and hoses for wear and tear. Replace damaged components to maintain safety.
- Calibration Checks: Occasionally, calibrate your machine according to the manufacturer’s recommendations to ensure accuracy in welding.
Customer Reviews and Testimonials
User feedback plays a vital role in understanding the true performance of any product, and the Unimig Viper series is no exception. Let’s explore what users are saying.
What Users Say About the Unimig Viper
Many users have praised the Unimig Viper series for its versatility and reliability. Common positive remarks include:
- Ease of Use: Beginners highlight the user-friendly interface and automated settings that help them ease into welding.
- Performance: Many professionals emphasize the consistent performance across all welding processes, making it a dependable tool for varied jobs.
- Portability: Users appreciate the lightweight design, making it easy to transport for on-site work.
Critical Reviews: Common Concerns
Despite the overwhelmingly positive reviews, some users have raised concerns:
- Limitations in Duty Cycle: Some users feel the duty cycle for specific models could be limiting for heavy industrial applications.
- Need for Additional Equipment: A few users mentioned needing additional accessories, such as dedicated tanks for TIG welding, impacting initial cost.
FAQs about the Unimig Viper
As with any product, potential users often have questions. Here are some frequently asked questions regarding the Unimig Viper:
- Can the Unimig Viper 185 weld aluminum? Yes, the Viper 185 supports aluminum welding with the correct setup and wire.
- What warranty does the Unimig Viper series offer? Typical warranty offerings vary between models, often ranging from one to three years depending on registration.
- Is support available for troubleshooting? Yes, Unimig offers extensive customer support and online resources for troubleshooting and maintenance advice.
Leave a Reply