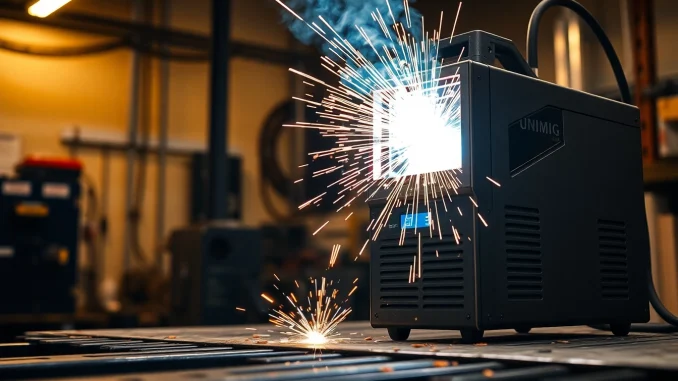
Understanding the Unimig TIG Welder
TIG (Tungsten Inert Gas) welding is one of the most precise welding methods, allowing for a high degree of control over the welding process. If you’re looking to expand your welding capabilities with precision and quality, investing in a unimig tig welder is a smart choice. This article will explore the features, benefits, and best practices for mastering your Unimig TIG welder.
What is a TIG Welder?
A TIG welder uses a non-consumable tungsten electrode to produce the weld. This method is known for its ability to create strong and precise welds on a variety of materials, including aluminum, magnesium, and stainless steel. Unlike MIG (Metal Inert Gas) welding, which uses a wire that becomes part of the weld, TIG welding requires the welder to feed a filler rod manually.
This process offers significant flexibility, especially in thin materials, and results in high-quality welds with minimal spatter. TIG welding is favored in applications requiring cleanliness and aesthetics in the weld joint, making it ideal for industries such as aerospace, automotive, and art-metal fabrication.
Key Features of Unimig TIG Welders
Unimig offers a range of TIG welders that cater to both beginner and advanced welders. Key features of Unimig TIG welders include:
- High-Frequency Start: Ensures a smooth arc initiation, reducing contamination and improving efficiency.
- AC/DC Capability: Allows for welding on a variety of metals including aluminum and steel.
- Adjustable Amperage Settings: Provides precise control over the heat input, crucial for thin materials.
- Portability: Many models are lightweight, enabling easy transport and use at different job sites.
- Digital Displays: Enhance user experience by providing real-time feedback on settings.
Benefits of Using a Unimig TIG Welder
Using a Unimig TIG welder offers numerous benefits:
- Precision: The ability to finely control the weld pool results in cleaner welds, which is essential for intricate work.
- Versatility: Unimig models can weld various materials and thicknesses, making them suitable for a wide range of projects.
- Quality of Welds: TIG welding produces high-strength welds, making it ideal for critical applications.
- Less Cleaning: The process reduces contamination and spatter, leading to less prep work after welding.
Choosing the Right Unimig TIG Welder for Your Projects
Comparison of Unimig Viper and Razor Models
The Unimig Viper and Razor series offer distinct features catering to different user needs. The Viper series is designed with user-friendly functionality, making it ideal for hobbyists and less experienced welders. It includes helpful setup guides to simplify operations.
In contrast, the Razor series is more focused on professional use, featuring robust components and advanced controls which allow for greater adjustments and capabilities. For example, the Razor 200 AC/DC welder includes superior welding technology, suitable for industrial applications.
Factors to Consider Before Purchase
When selecting the right Unimig TIG welder, consider the following factors:
- Welding Material: Identify the types of materials you will be working with, as some models are optimized for certain metals.
- Power Source: Determine whether you need an AC or DC welder based on your material requirements.
- Portability: Assess the weight and design if you need to transport your welder frequently.
- Budget: Weigh the features you need against the cost of the machine. Investing in a higher-end model may save money in the long run due to its capabilities.
Common Applications for Unimig Welders
Unimig TIG welders are versatile enough for a wide range of applications:
- Aerospace: Used for welding thin-walled structures where precision is critical.
- Automotive: Essential for high-strength components and intricate designs, such as architectural parts.
- Art and Sculpture: Artists use TIG welding for its clean welds that require a high level of detail.
- Maintenance and Repair: Ideal for repairs on various equipment due to its flexibility.
Getting Started with Your Unimig TIG Welder
Essential Accessories for TIG Welding
To get the best performance from your Unimig TIG welder, consider investing in these essential accessories:
- Tungsten Electrodes: Select the right diameter and type based on your welding needs.
- Filler Rods: Ensure you have compatible filler rods that match the base metals being welded.
- Welding Gloves: Protect your hands with appropriate heat-resistant gloves.
- Protective Gear: Use proper helmets and safety goggles to prevent injury from harmful UV rays and sparks.
- Gas Supply: Ensure that you have a reliable argon gas supply for shielding the weld.
Safety Precautions While Welding
Safety is paramount in any welding operation. Here are some essential safety measures:
- Wear Proper Gear: Always wear gloves and a welding helmet, and consider a full-body suit to cover skin.
- Ventilation: Ensure proper ventilation in your workspace to dissipate harmful gases.
- Check Equipment: Regularly inspect your welder, hoses, and connections to prevent leaks.
- Fire Safety: Keep a fire extinguisher nearby and ensure the welding environment is clear of flammable materials.
Setting Up Your Workspace
Creating an effective workspace can significantly enhance your productivity while welding. Consider these tips:
- Organize Tools: Keep all tools and accessories within reach and organized.
- Work Surface: Use a sturdy table or bench that can withstand heat and sparks.
- Lighting: Ensure your workspace is well-lit to avoid accidents and enable precision.
- Power Source: Ensure that your welder is connected to a suitable power source with appropriate outlets.
Techniques to Improve Your TIG Welding Skills
Fundamentals of TIG Welding Techniques
Mastering the fundamentals of TIG welding is crucial for long-term success. These include:
- Arc Control: Practice maintaining a consistent arc length to prevent burning through the material.
- Heat Management: Control the heat input to avoid warping and ensure proper metal fusion.
- Movement Patterns: Develop consistent movement patterns, such as circular or zigzag motions, to achieve uniform bead shapes.
- Filler Rod Handling: Learn to feed the filler rod smoothly into the weld pool without disturbing the arc.
Advanced Welding Techniques Using a Unimig TIG Welder
As your skills develop, there are more advanced techniques to explore:
- Pulsed TIG Welding: This technique uses pulsed current to control the heat, allowing for better control over the weld pool.
- TIG Welding with Foot Pedal: Using a foot pedal allows for dynamic control of amperage, which can enhance comfort and accuracy.
- TIG Welding in Different Positions: Practice welding in various positions (flat, horizontal, vertical) to diversify your skills.
Common Mistakes and How to Avoid Them
Identifying common mistakes can improve your welding process:
- Inadequate Cleaning: Always clean the metal surface thoroughly to prevent contamination of the weld.
- Improper Settings: Ensure that your settings match the requirements of the material; refer to manufacturer guidelines or charts.
- Inconsistent Travel Speed: Maintain a steady speed to avoid undercutting or excessive buildup of weld material.
Maintenance and Troubleshooting for Unimig TIG Welders
Routine Maintenance Tips
Regular maintenance is essential to keep your Unimig welder functioning optimally:
- Cleaning: Regularly clean the welder and accessories, especially the torch and collet body.
- Inspecting Cables: Check for any signs of wear or damage to cables and hoses.
- Tungsten Replacement: Replace the tungsten electrode as needed, particularly after heavy use.
Diagnosing Common Issues
Understanding how to identify and resolve issues can prevent downtime:
- Weld Not Penetrating: Check the welder settings; you might need to increase the amperage.
- Inconsistent Arc: This could be due to contaminated tungsten or improper gas flow; ensure both are addressed.
- Excessive Spatter: Review the travel speed and filler rod technique to achieve cleaner welds.
When to Seek Professional Repair Services
If you encounter persistent issues that cannot be resolved through routine maintenance, it may be time to consult with a professional. Signs that indicate the need for repair include:
- Electrical Issues: If the welder does not start or displays error codes, a professional diagnosis may be necessary.
- Overheating: Continuous operations where the welder overheats regularly point to an internal issue.
- Unusual Noises: Strange sounds during operation may signal mechanical failure.
Leave a Reply