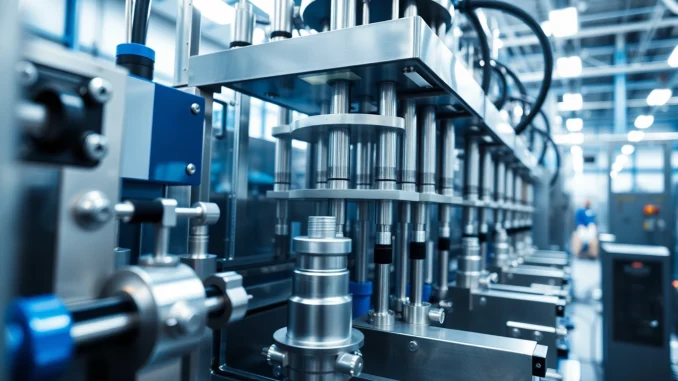
Introduction to Filling Machines
In the world of packaging and manufacturing, filling machines play a crucial role in ensuring efficiency and accuracy. These machines are designed to accurately dispense liquids, powders, or granular products into containers, enhancing productivity and maintaining product integrity. As industries strive for increased automation and speed in their processes, understanding the functionalities and types of filling machines becomes essential. For those seeking reliable equipment to streamline their production lines, partnering with a Filling Machine Supplier can be a game-changer.
What is a Filling Machine?
A filling machine is a device that automatically fills containers with a specified volume of product. Depending on the machine’s design, it can be used for a variety of products, including liquids, powders, and granules. These machines are essential in various sectors such as food and beverage, pharmaceuticals, cosmetics, and chemicals, ensuring that products meet the required standards before reaching consumers.
Types of Filling Machines
Filling machines can be categorized based on several criteria including the type of product, level of automation, and operational mode. The main types include:
- Liquid Filling Machines: Used for filling containers with liquids ranging from water to viscous substances such as oils or creams.
- Powder Filling Machines: These machines handle dry products like powders, granules, and small pellets, making them ideal for pharmaceuticals and food products.
- Gravity Filling Machines: Rely on gravity to fill containers and are suitable for low-viscosity liquids. They can be manual or automated.
- Pneumatic Filling Machines: These use compressed air to transfer liquids into containers, offering flexibility for various product viscosities.
- Vacuum Filling Machines: Typically used for more sensitive products, these machines ensure that each container is filled optimally without air bubbles.
- Auger Filling Machines: Specifically designed for powdery substances; they dispense product using a screw mechanism.
Importance of Choosing a Reliable Supplier
When investing in filling machines, the importance of selecting a reliable supplier cannot be overstated. A good supplier provides not only high-quality equipment but also support in terms of installation, maintenance, and ongoing service. Moreover, a dependable supplier understands industry standards and can provide machines that comply with regulatory requirements, ensuring that production processes remain seamless.
Benefits of Partnering with a Leading Filling Machine Supplier
The benefits of working with a well-established filling machine supplier go beyond just acquiring the necessary equipment. Here are several advantages:
Quality Assurance and Performance
Leading suppliers invest in research and development, ensuring that their machines are built to last and operate at optimal efficiency. When you partner with a reputable filling machine supplier, you benefit from:
- Durability: High-quality components lead to reduced breakdowns and maintenance issues.
- Precision: Automated systems provide consistent filling, reducing product waste and errors.
- Compliance: Adherence to industry standards ensures that products are filled safely and correctly.
Customer Support and Service
Access to reliable support services is crucial for any manufacturing operation. Effective customer support can significantly enhance operational efficiency. This includes:
- Installation Services: Professional installation reduces the risk of operational issues post-purchase.
- Training: Suppliers often provide operator training to ensure that your team understands the equipment fully.
- Technical Support: Ongoing support to troubleshoot issues quickly and minimize downtime.
Technological Innovations in Filling Machines
Leading suppliers are continuously innovating, integrating the latest technologies into their filling machines. This includes features like:
- Smart Technology: IoT capabilities allow for real-time monitoring and data collection for analytics and optimization.
- Energy Efficiency: Modern machines are designed to consume less power without sacrificing performance.
- Integration Capability: Ability to connect with other machinery and systems for a fully automated production line.
Key Features to Look for in Filling Machines
Choosing the right filling machine entails considering several key features to ensure the machine meets your production needs:
Automation Capabilities
Automation can drastically improve operational efficiency. It’s essential to evaluate:
- Level of Automation: Manual, semi-automatic, or fully automatic systems based on production volume and budget.
- Speed: The machine’s fill rate should align with your production goals.
- Repeatability: Ensuring each fill is consistent is vital for product quality.
Customization Options
Every operation has unique requirements. Look for suppliers that offer:
- Modular Designs: Customizable features to accommodate different container sizes and shapes.
- Selectable Filling Volumes: Options to set different fill sizes depending on production runs.
- Material Compatibility: Machines that can handle a variety of product types from sensitive liquid to abrasive powders.
Compatibility with Various Products
Your filling machine should be versatile enough to handle different products. Key considerations include:
- Viscosity: Different machines are suited for various product viscosities, from water-like liquids to thick pastes.
- Container Types: Compatibility with bottles, jars, pouches, and cans is crucial for versatility in packaging.
- Environmental Conditions: Machines should operate efficiently in various environments, whether cold, warm, or humid.
Case Studies: Successful Implementations
To understand the practical application of filling machines and the benefits of partnering with the right supplier, consider the following case studies:
Industry-Specific Applications
1. Food and Beverage Sector: A leading beverage manufacturer partnered with a supplier to upgrade to fully automatic filling machines. This transition resulted in a 30% increase in production speed and 98% reduction in waste due to overfills.
2. Pharmaceutical Industry: A pharmaceutical company implemented a new powder filling machine that offered high precision and compliance with strict regulations. This change improved product safety and significantly reduced human error.
Client Testimonials
Feedback from clients using advanced filling machines highlights their satisfaction:
“Since implementing the new filling technology, we have seen noticeable improvements in productivity and quality control. Our partnership with the supplier has been invaluable.” – Production Manager, Leading Cosmetic Company
Performance Metrics Post-Implementation
Post-implementation metrics often reveal significant improvements:
- Increased Output: Many companies report up to a 50% increase in output within the first few months of upgrading their machines.
- Reduced Downtime: Advanced filling machines have lower mechanical failure rates, leading to fewer maintenance disruptions.
- Enhanced Quality: Precision filling results in fewer customer complaints and returns due to inconsistencies.
Choosing the Right Filling Machine Supplier
Choosing the right filling machine supplier requires careful evaluation and strategic thinking. Here are some important considerations:
Evaluating Supplier Reputation and Experience
Determine the reliability of a supplier by:
- Researching Feedback: Examine reviews and case studies from past customers.
- Industry Track Record: How long have they been in business, and what sectors do they serve?
- Certifications: Ensure that the supplier’s products meet industry standards and regulations.
Negotiating Terms and Pricing
When discussing terms with potential suppliers, focus on:
- Warranty Terms: Understand the warranty coverage for their machines.
- Prices and Financing Options: Be clear on what is included in pricing and explore any payment plans or financing options.
- Service Contracts: Clarify maintenance and support services covered in your agreement.
Building Long-Term Partnerships
The goal should be to cultivate a long-term relationship with your filling machine supplier. Key strategies include:
- Communication: Regularly discuss performance and potential upgrades or changes needed.
- Feedback Loop: Provide constructive feedback on machine performance to foster improvements.
- Joint Development: Collaborate on upcoming projects to develop bespoke solutions that meet specific challenges.
Leave a Reply