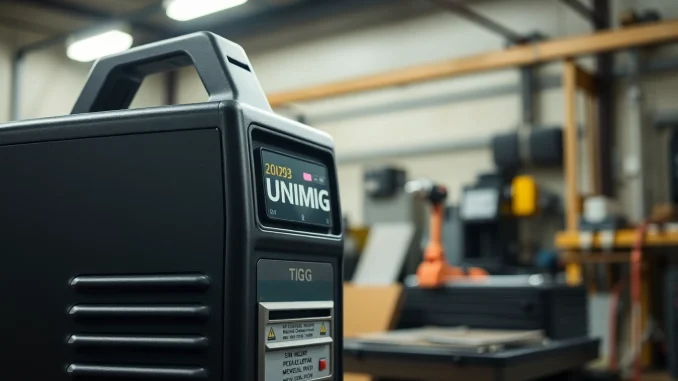
Understanding the Basics of Unimig TIG Welders
What is a Unimig TIG Welder?
A unimig tig welder is a specialized tool designed for precision welding. Using the Tungsten Inert Gas (TIG) process, these welders represent one of the most effective welding technologies due to their ability to produce high-quality welds. The implement of TIG welding involves utilizing a non-consumable tungsten electrode to produce an arc that melts the base metal. This method is popular across various industries for its versatility and ability to weld thin materials with exceptional control over heat input and weld appearance.
Key Advantages of Using Unimig TIG Welders
One of the standout features of Unimig TIG welders is their ability to offer precise control over the welding process. This precision allows for a clean weld, making it ideal for applications where appearance is crucial, such as automotive or artistic metalwork. Other advantages include:
- Versatility: Unimig TIG welders can work with a diverse range of materials including aluminum, magnesium, copper, and stainless steel.
- Clean Welding: The process generates less spatter and produces a tidy and aesthetically pleasing weld.
- Adaptability: The ability to control the heat input means that it can be used on thin metals without burning through.
- Minimal Distortion: TIG welding results in less warping of the materials being welded compared to other methods.
Applications of TIG Welding in Various Industries
TIG welding is widely regarded as a versatile welding method, applicable in several sectors:
- Automotive: Used for creating lightweight and strong components in vehicles, particularly in race cars and custom builds.
- Aerospace: Critical for projects that require extreme durability and reliability, KEY in the production of airframes and engine parts.
- Art and Fabrication: Artists and metal fabricators benefit from the clean and aesthetic properties of TIG welds, allowing for intricate designs.
- Manufacturing: Ideal for creating high-precision components with a low tolerance for error, such as medical devices and instruments.
Choosing the Right Unimig TIG Welder for Your Needs
Comparing Models: Viper vs. Razor
Among the Unimig TIG welders, the Viper and Razor models stand out as two popular picks. The choice between these models largely depends on specific needs and work environments. The Viper series includes models such as the VIPER 180 AC/DC Mk II, which is known for its powerful capabilities across various materials. Users appreciate this model for its user-friendly features designed for both beginner and experienced welders.
On the other hand, the Razor series, like the RAZOR TIG 200 AC/DC, is geared more towards professional applications, delivering robust performance for industrial welding tasks. Key differences to consider include:
- Functionality: Viper models are oriented towards hobbyists and small workshops, while Razor models cater to industrial use.
- Heat Control: Razor welders often offer advanced features allowing finer adjustments, beneficial for more complex projects.
Features to Look for in a Unimig TIG Welder
When selecting a Unimig TIG welder, consider the following features:
- AC/DC Capabilities: The ability to switch between alternating current (AC) and direct current (DC) expands the welder’s usability across different materials.
- Amperage Range: A wide amperage range allows you to tackle various thicknesses of material effectively.
- Control Panel: Look for models with user-friendly interfaces that provide easy access to settings and adjustments.
- Weight and Portability: Depending on your workspace, a portable welder may be necessary for efficiency and accessibility.
- Cooling System: Proper cooling mechanisms prolong the welder’s life and enhance performance during heavy duty cycles.
Understanding AC/DC TIG Welding Capabilities
AC/DC capabilities in TIG welding allow for versatility in working with different materials. AC welding is primarily used for aluminum and magnesium, enabling welders to produce clean and strong welds without contaminating the material. On the other hand, DC is ideal for ferrous metals and provides better penetration due to its steadier current flow.
Choosing a welder with both AC and DC capabilities ensures that you are equipped for a broader range of applications, which is beneficial for those working in diverse fields or for those who wish to expand their project scope.
Setup and Operation of Unimig TIG Welders
Essential Setup Steps for Optimal Performance
Setting up your Unimig TIG welder correctly is crucial to ensure efficient operation and high-quality welds. Here’s a step-by-step guide:
- Ensure that the workspace is clean and appropriate for welding environments.
- Check the gas supply and ensure that the gas bottle is properly connected. If using argon, ensure it is at the right pressure.
- Set up the welder’s integral components, such as the torch and ground clamp, securely on the workpiece.
- Adjust the amperage settings based on the material thickness you are working with.
- Perform a test weld on a scrap piece to ensure proper settings before commencing work on your actual material.
Common Mistakes When Using Unimig TIG Welders
Even experienced welders can make mistakes that affect the quality of their work. Common errors include:
- Improper gas settings can lead to contamination of the weld area.
- Inadequate cleaning of materials prior to welding can result in defects.
- Not performing a test weld can lead to unwanted outcomes on actual projects.
- Using wrong tungsten electrode sizes for the material being welded can reduce the effectiveness of the weld.
Safety Tips for Welders
Safety should be a top priority while operating a TIG welder. Here are key safety tips:
- Always wear appropriate personal protective equipment (PPE), including a welding helmet, gloves, and protective clothing.
- Ensure that the workspace is well-ventilated to avoid inhaling harmful fumes.
- Keep a fire extinguisher nearby and ensure no flammable materials are within reach of the welding activity.
- Be aware of your surroundings and ensure that no one else is within hazardous reach while you are welding.
Maintenance Tips for Your Unimig TIG Welder
Routine Checks to Ensure Longevity
Regular maintenance of your Unimig TIG welder is essential to prolong its lifespan and maintain performance. Consider the following routine checks:
- Inspect electrical connections and cables for wear or damage regularly.
- Clean the gas nozzle and contact points to prevent contamination.
- Check the integrity of the torch and replace any worn components.
- Monitor the gas flow and refill gas cylinders as needed to avoid interruptions during welding.
Troubleshooting Common Issues
Even with regular maintenance, you may face challenges with your welder. Here are a few common issues and troubleshooting tips:
- Inconsistent Arc: Check for proper gas flow, ensure clean tungsten, and verify correct amperage settings.
- Excessive Spatter: This may indicate incorrect settings or contamination; adjust gas flow and ensure proper material preparation.
- Weak Welds: Check that you are using the appropriate electrode and amperage for the thickness of the material.
When to Seek Professional Repairs
If issues persist despite your troubleshooting efforts, it may be time to seek professional help. Things like electrical failure or internal component damage often require expert intervention. Schedule regular professional maintenance checks to prevent long-term damage and costly repairs.
Future Trends in TIG Welding Technology
Innovations in Unimig TIG Welding Equipment
The welding industry is on a rapid technological evolution, with Unimig leading the charge with its innovative approaches. Future advancements may include:
- Smart Welding Technology: Integration of IoT capabilities to provide real-time monitoring and suggestions for optimal settings.
- Advanced Materials: Development of welders capable of working with emerging materials such as composites and super alloys.
- Robotic Automation: As automation increases, the incorporation of robotics for precision welding applications is anticipated to become more prevalent.
Industry Insights: Where Is Welding Technology Heading?
Insights suggest that welding technology is trending towards increased automation and integration with artificial intelligence to improve precision and efficiency. The demand for more complex and high-strength welding applications is driving innovation, especially in sectors like aerospace and automotive.
The Impact of Automation in TIG Welding
Automation stands at the forefront of the welding industry’s future. TIG welding robots can provide consistent quality and reduce human error, allowing for higher production speeds without sacrificing the quality or aesthetics of the weld. As these technologies become more accessible, they offer businesses cost savings and efficiency improvements.
Leave a Reply